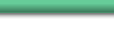
2:UV印刷に必要なもの(UVインキ・UV照射装置)
UV印刷にはUVインキと、それを硬化乾燥させるUV照射装置が必要です。
[UVインキ(=紫外線硬化型インキ)]
UVインキとは、紫外線(UV)を照射すると秒速で硬化する無溶剤型インキです。
一液型(一般的UVインキ)、二液型、熱併用型、水性型、その他、仕上がり状態から
グロス(艶あり)とマット(艶消し)、塗膜性質からソフトタイプ(追従型)/ハードタイプ(剛性型)、
黄変/無黄変形と分類することもでき、社会ニーズにあわせて様々に工夫されています。
UVインキの基本となる樹脂は、「オリゴマー(プレポリマー)」といわれるもので、
低粘度な液状
から半固体状まであり、代表種としてポリエステルアクリレート、エポキシアクリレート、ウレタン
アクリレートなどがあります。そのため、基本的にウレタンアクリレート等には「くいつきがいい」
のも特徴です。
その他UVインキの主成分は、光重合性樹脂(=速硬化のアクリレート系オリゴマー/モノマーが主流)、
光重合開始剤、顔料、重合禁止剤、消泡剤、帯電防止剤などで、原則的に有機溶剤は含まず、
低粘度のオリゴマー・モノマーなど反応性希釈剤=レジューサーで粘度を調整します。
UVインキの濃度調整方法
一般のUVインキはそのまま印刷することを前提とした粘度で出荷されていますが、
粘度を下げたい場合は各専用のレジューサーを10%以内で添加します。
粘度を上げたい場合は高粘度のメジウム(マットクリアーなど)を添加します。
UVインキの安全性
UVインキは、蒸発物や溶剤がないので吸入による心配はありません。
付着すると皮膚刺激性があるので保護手袋を着用し、皮膚に付着したときは洗い落とします。
UVインキの貯蔵について
UVインキは、貯蔵中に光が当たらなくても、熱によりゲル化して固まることがありますので
冷暗所に保管します。また時々インキを攪拌して空気を混入してやります。
(インキ中に発生する『反応活性』は、空気中の酸素により非活性化する)
きちんと管理すれば2年は貯蔵可能といわれていますが、半年を目処にするのが無難です。
[UV照射装置]
UVインキを乾かすためにはUV照射装置が必要ですので、
UV照射装置を 今の印刷設備に付け足します。
予算がある場合はコンベア一体型などの専用照射装置を使います。
導入経費を抑えるためにはUV照射用灯具と電源をセットで用意します。
灯具にシャッター機能やコールドミラーなど、すぐ使うための機能を組み込んだ
クリップオン型装置や、[卓上バッチ/コンベア搭載]の、2種類の使い方を選べる
装置もあります。
弊社は、お客様のご要望にあわせたUV硬化装置・UV硬化ラインの設計・製造を
得意としておりますので、大型の製造ラインから小型のユニットまで、最適の製品を
リーズナブルに御提案させていただきます。

*耐熱性の低い印刷素材はUVランプからの熱で変形を起こすので、
この熱を減らす工夫を装備に足します。
その代表が開閉シャッター機能とコールドミラーです。
コールドミラーは紫外線のみを反射、可視光線や赤外線の殆どは透過させて、
印刷素材への直接的な熱の影響を抑えます。
その他熱対策としてはコールドフィルターをランプ下に置く、
本体ボードを冷却する水冷ボードなど様々な方法があります。
UV照射用灯具で使われるランプの種類
ランプは、高圧水銀灯とメタルハライドランプが主で、超高圧水銀灯や
キセノンランプはランプ寿命や紫外線量、ランプ長の点であまり選ばれません。
インキの硬化性に大きな影響を及ぼすのは、ランプの発光波長の分布です。
UVランプは紫外線の他に可視光線や赤外線も発光しており、その中でUVインキの
硬化に有効な波長域は300〜400nmと考えられています。
これは長波長の方が透過性に勝っていることと、UVインキに使用される顔料が
365nm近くに最大透過率を示すものが多用されていることによります。
そのため膜厚の厚い印刷の場合には、長波長の発光量が多いメタルハライドランプが
内部硬化性に優れているため有利です。
UVインキとUV照射のマッチング・テスト方法
UVインキへの照射条件を決定するためには必ず実際に近い条件下でテストをします。
印刷素材も本生産に使われるものを使用し、所定の照射条件で硬化させた後、
印刷面のアフタータック(指触による)、
接着性(碁盤目テープ法)、
耐引掻性(爪、鉛筆)
折曲げ耐性
などの試験を行い、照射条件や印刷膜厚を調整します。
照射条件
1. 前提条件(プロダクツ特有のUV波長特性・熱対策の必要性など)
2. 照射幅
3. 積算光量(ランプ強度・コンベア速度との兼ね合い)
4. プレヒート等前後プロセスの有無
5. 設置スペース等
があり、特に前提条件への一致と、積算光量が重要です。
|